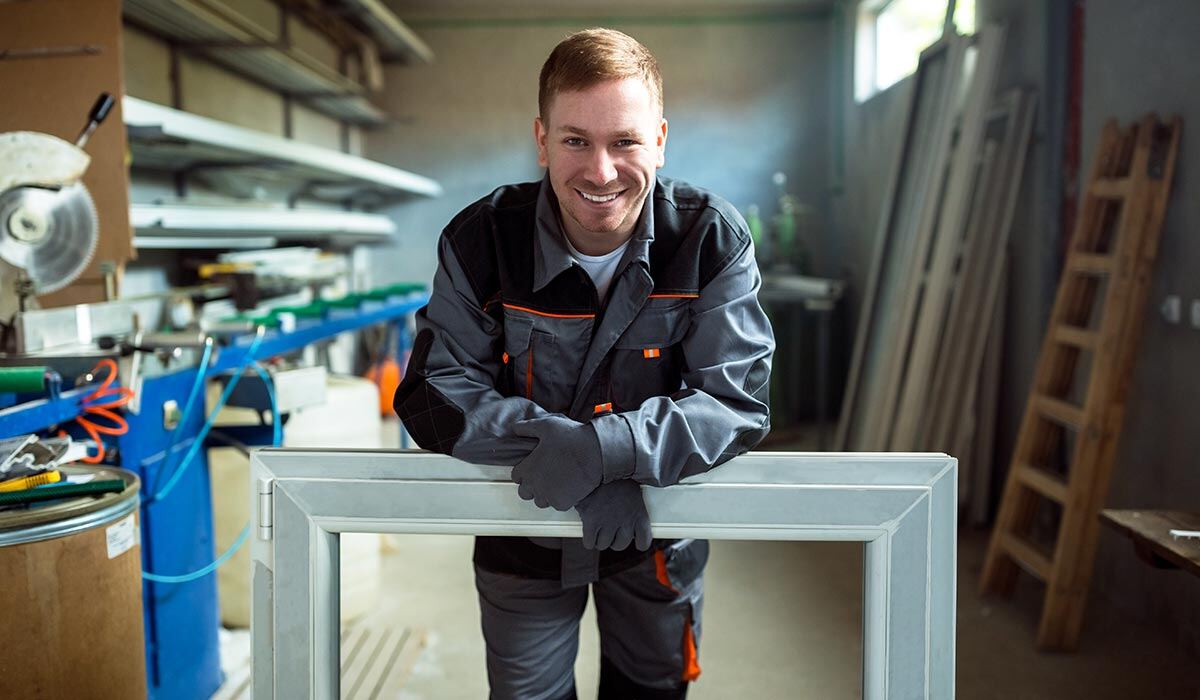
Automatic set up of machine: less time, more efficiency
Automatic set up of machine: all the advantages
Starting with set-up procedures, automated systems will speed up the preparation of each job and ensure meas If we asked you to list your business objectives in order of priority, almost certainly we would find the word efficiency high on the list.
There are many ways to improve efficiency and our way of supporting a customer’s production efficiency is an intrinsic part of the solutions we design for profile wrapping and lamination.
With production efficiency as a driver, we have developed equipment and systems that prioritise automation. Companies looking to increase their efficiency and profitability will find us to be a partner that understands their priorities and delivers proven solutions tailored to their individual needs.
Automation ensures faster set-up times, greater process safety, reproducible quality, less manual labour. All this adds up to increased productivity and enhanced quality.
urable accuracy. With an increasing number of low-volume production runs, the shorter set-up times are vital to keep costs to a minimum.
Here are a few key benefits:
- shorter set-up times > more time for production
- automatic, parameter-based set-up > reproducible quality and consistent output
- fully automatic set-up > no need for skilled labour on this task
- automatic, parameter-based set-up > uniform, waste-free primer application
- accurate set-up and processing > fewer re-works required, increased customer satisfaction.
Reducing times with the automatic set-up
When changing profile geometry, set-up becomes an unavoidable part of the production process. Changing the decorative material also generates downtime. Machines are stopped in both cases, and productivity is affected. Moreover, materials are lost each time you stop: adhesive, decorative and core materials.
Smart devices which support automated solutions are able to minimise set-up times and enhance productivity. Our efforts to boost your productivity by reducing set-up times are integrated into several Duespohl machines. More details here
Automatic set up of machine: the Düspohl solutions
So which devices or automation systems are key to reducing set-up times and making your factory much more productive?
PrimeStar
Felt strip application systems for adhesives generate downtime as you need to cut the strips for each profile geometry change. Our automated PrimeStar works with profile-specific application heads, and changing from one profile geometry to another takes just 20 seconds.
ReelChange
This is an automatic reel change system applied to a double unwinding station. Moving from a single unwinder to double already means you can avoid interruptions to production. The automatic reel changer additionally enhances productivity by taping in-sequence reel ends together during production.
ReelWizard
This device is perfect for batch one jobs, making it possible to produce at a normal speed even if each profile in the process is wrapped with a different foil. Probably the most flexible automatic solution which can be used to boost productivity and respond to today’s market trends.
FastChange
This system accelerates preparation of the wrapping process. Further to the quick-fix system enabling fast, tool-free pressure roller positioning, FastChange is a solution for entire sets of pressure rollers. Base on hydraulics, it locks the roller holders and helped by colour-coding, operators can identify sets of bars according to profile geometry, implementing changes without wasting time.
Ask the experts!
Automation is a game changer and can support your business activities in terms of increased productivity and more consistent quality. Over the years, based on our in-depth experience in wrapping technologies, we have developed several automatic solutions.
Contact us and one of our experts will advise you on which solution to choose for your specific needs.