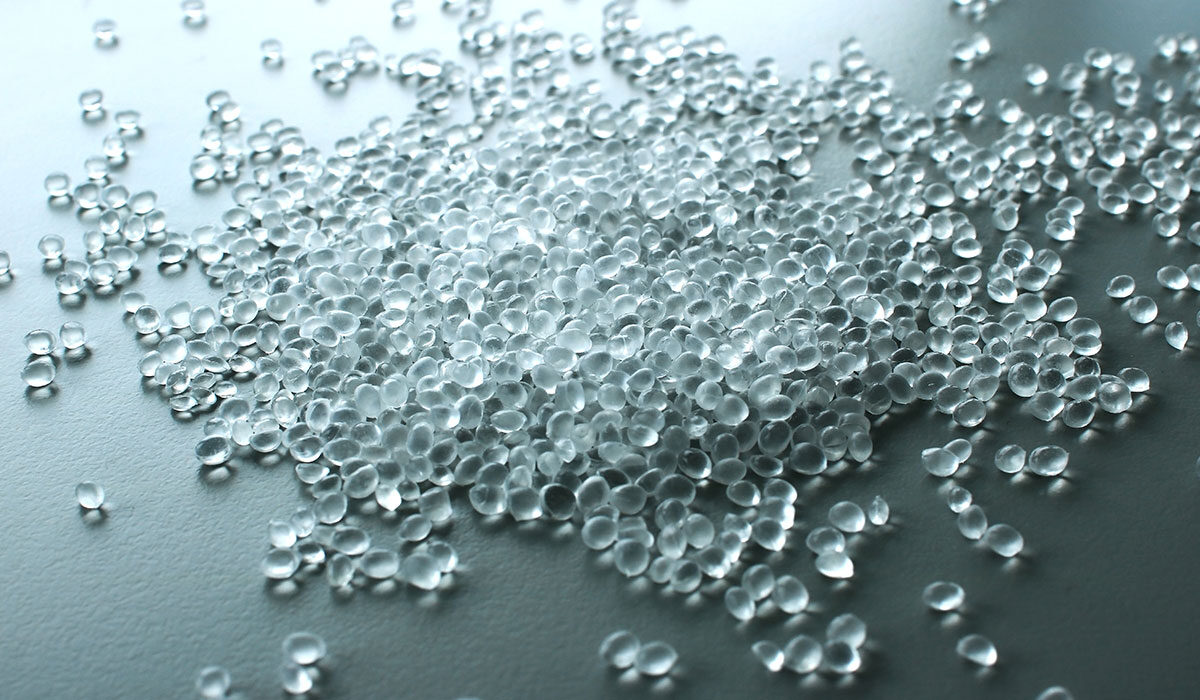
Hot melt application system: less glue, more quality
Glue application is an essential operation that must be accomplished in any wrapping or lamination line. In order to optimise the overall process, a hot melt application system can be integrated into the line, even as a retrofit. Düspohl delivers a slot coater solution as well as pre-melters for PUR (Polyurethane), PO (Polyolefin) and EVA (Ethylene-Vinyl Acetate) adhesives.
Our slot coater glue application system uses a patented slot nozzle without a gasket and with no spare part needs, handles a wide range of processing widths and works with all surface materials on reels.
Our melting units are designed to minimise maintenance and spares, they melt only the required glue on-demand, and feature energy-saving technologies to cut costs and improve sustainability.
Hot melt application system: all the advantages
Combining our melting units with our glue application system ensures a series of advantages that will affect the efficiency and cost-effectiveness of today’s wrapping and lamination lines. Pre-melters are designed to process only the required amount of glue and avoid burning issues. Freshly melted glue always performs better and on-demand melting saves glue consumption and related costs. Pre-melters also play a key role in supporting production efficiency, so these units adapt to production speeds and can be refilled with PUR blocks or EVA or PO granules in time to avoid stoppages.
The glue application system itself is a crucial element in which the glue is constantly in motion. Our slot coater system is designed to apply glue in a uniform fashion, and is shaped to prevent burning of the adhesive which flows continuously.
Düspohl’s hot melt glue application system
The slot coater is the heart of glue application system, fed with adhesive from the pre-melter. Our SlotCoater uses slot nozzle with a patented design that ensures uniform distribution of the adhesive on the decorative material. With no gasket and no valves present, and made of highly resistant alloys, it will last a lifetime and requires no maintenance or replacement of parts.
It is particularly recommended for high-gloss thermoplastic surface materials and application widths can be adjusted between 250 and 1400 mm. SlotCoater can be installed as a retrofit to improve line efficiency and optimise glue consumption.
UniMelt: power, efficiency and reliability
UniMelt is our energy-efficient pre-melter for EVA and PUR granular adhesive or blocks from 2 to 20 kg. In the case of PUR, the unit features a solution that prevents the curing process taking place prior to application. Melting capacity, depending ion adhesive type, is available for up to 40 / 80 / 160 kg/h and thanks to the absence of gaskets and seals, UniMelt is maintenance-free and highly reliable.
PowerMelt: for all granular hot melt adhesives
PowerMelt is easily integrated into our wrapping lines and represents a highly efficient melting solution for all granular adhesives. Low energy requirements (e.g. 7,5 kWh for 120 kg/h of EVA adhesive) and very short heating-up times make PowerMelt a cost-effective investment, increasing production efficiency and improving wrapping line sustainability. The extruder features a self-cleaning system to maintain excellent glue availability and glue temperature as it leaves the melting unit always corresponds automatically to the melting point of the adhesive used, thereby ensuring an interruption-free process. Melting capacity, depending adhesive type, is available for up to 600 kg/h.
Hot melt application system: how to choose one
Alongside our patented SlotCoater which ensures homogeneous glue application and cost-effective processing, our pre-melters, UniMelt and PowerMelt, can be integrated to increase line efficiency and guarantee consistent processing quality. With our vast experience and thousands of units installed worldwide, we are able to advise companies on the correct choice or combination of solutions according to their products, glues and specific needs. Contact us and ask for personalised advice.