RoboWrap Window
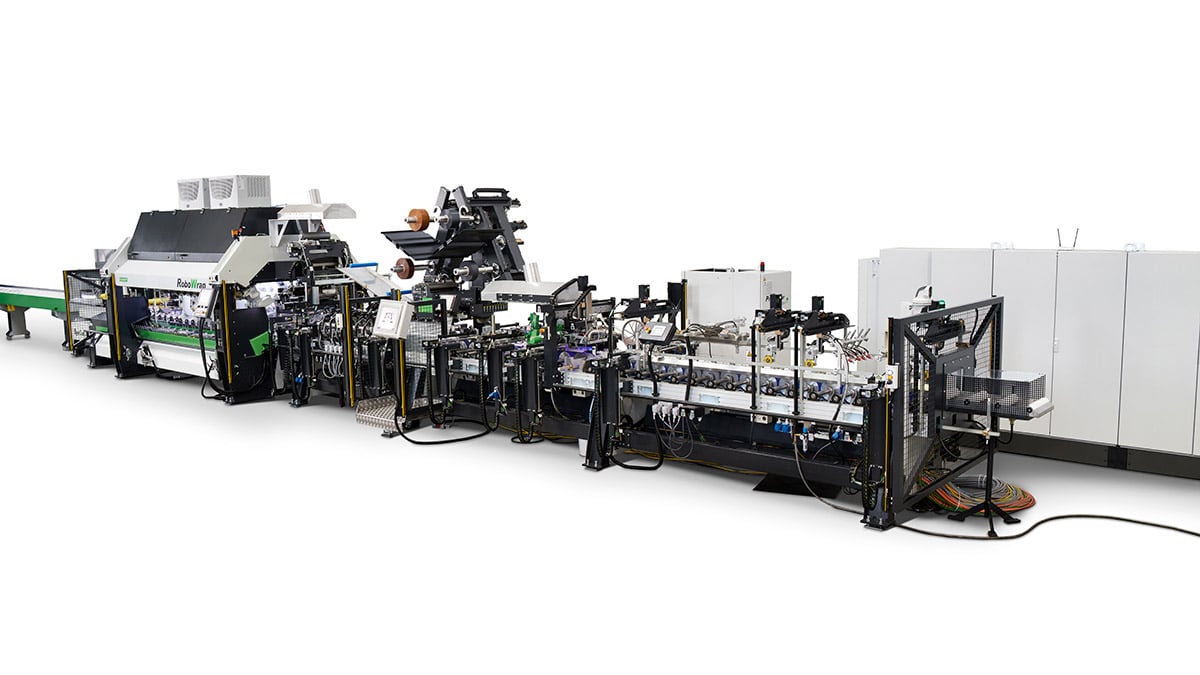
With its maximum degree of automation and digitisation, it is also Industry 4.0 implementation in the wrapping industry.
The RoboWrap‘s special software was developed in cooperation with the universities of Bielefeld and Paderborn, Mitsubishi Electric as well as the Fraunhofer IEM. In collaboration with customers and partners, our dedicated high-level programming department is constantly developing useful updates that respond to the market's needs.
Ideal for
- Window profiles
- Other PVC profiles
- Profiles made from metal
Would you like to receive a free consultation to find out if RoboWrap Window is the solution you need?
Contact us for a non-binding, first conversation.
Description
With this profile wrapper, you lower your set-up times dramatically. Once the positions of the pressure rollers have been programmed by the operator, the system repeats the settings fully automatically at any later time. Regardless of how different or similar the previous profile was, the robots perform the set-up for the new profile in no time! This does not only lead to a significant increase in production, but also to greater calculation security in the pricing of our customers. Since the intelligent software analyses the operator's procedure before each set-up process, it always comes to the desired wrapping result even with worn or modified pressure rollers.
An operator with knowledge of wrapping technology is able to transfer his knowledge to the intuitive user-friendly interface of the screen after a very short training phase and will be able to program the profile wrapper for the respective profile. For the further production runs itself, no specialist personnel will be needed.
After more than ten years of development and a local innovation award as well as the Innovation Award of Ligna fair, the first machines were delivered for the plastic as well as for the wood sector.
In order to benefit from the possibilities of artificial intelligent in profile wrapping, we are participating in a project funded by the Germany Ministry for Economic Affairs and Climate Action: The AI marketplace. And since the progress of technology never stops, further cooperation projects are being prepared.
The standard equipment on this series of machines includes:
-
Automatic reel changing system
-
Foil heating system
-
Air humidifier
-
Automatic web edge control
-
The maintenance-free, infinitely adjustable wide slot nozzle (Duespohl exclusive)
-
Speed and width-related dosing control (glue)
-
Powerful and efficient primer application systems: PrimeStar or DigiApp
-
Energy efficient premelter
-
Automatic format adjustment
-
Wrapping zone equipped with robots by Mitsubishi Electric
-
Highly intelligent, constantly evolving software
The optional equipment on this series of machines includes:
-
Infeed and outfeed systems
-
Reel changing system for batch size 1 ReelWizard
-
Protective foil unwinding unit
-
Synchronised separating systems
-
Automatic slot nozzle positioning
-
Process data logger with visualisation on touch screen and connection to your ERP
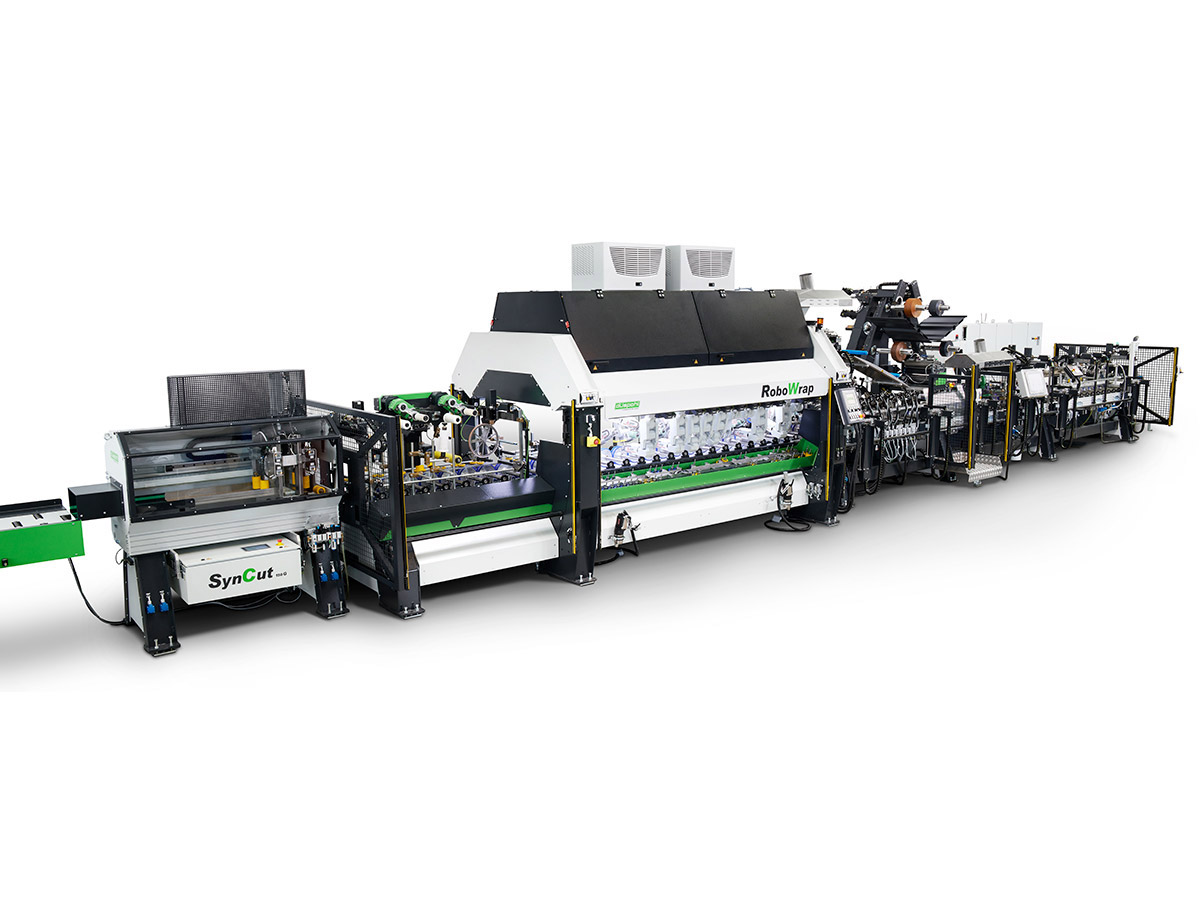
Possible configuration
RoboWrap Window featuring ReelWizard, a double unwinding unit for protective foil and SynCut 150G
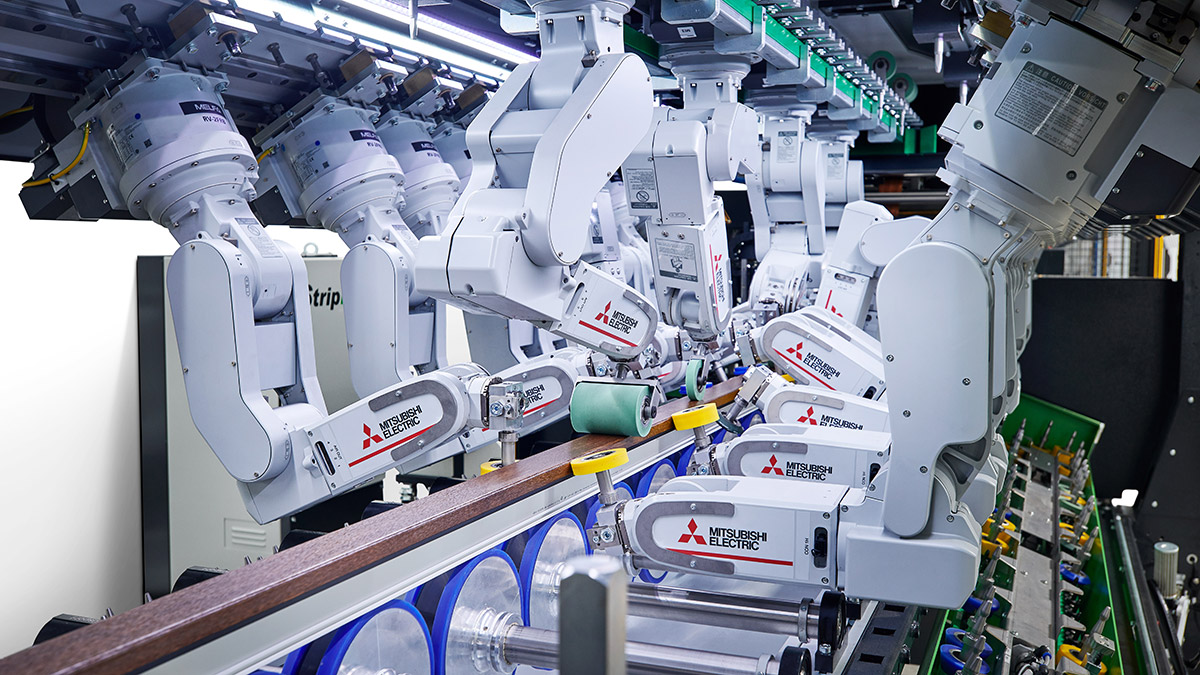
Close up wrapping zone
Featuring 24 robots to position the pressure rollers
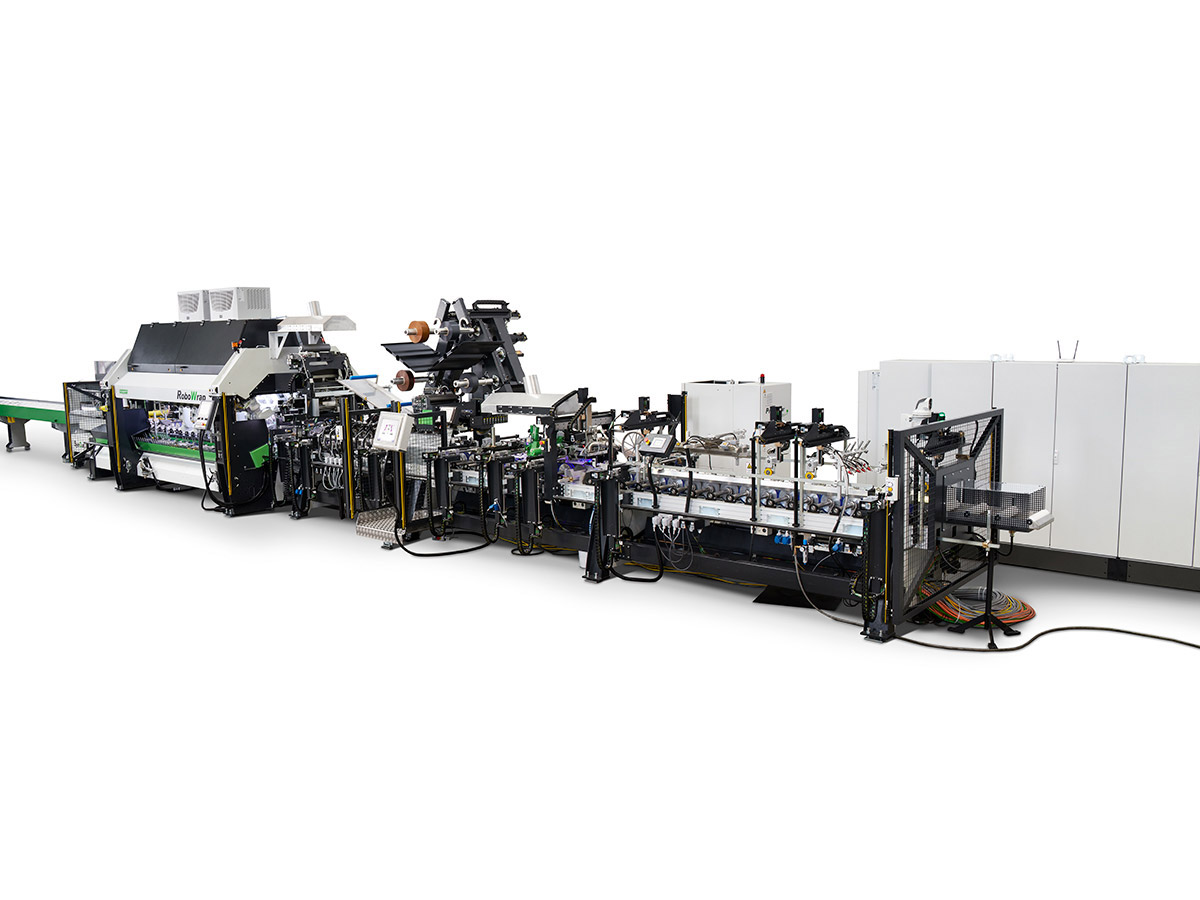
RoboWrap Window
Featuring automatic format adjustment, ReelWizard, PrimeStar and stand-alone electrical cabinet.
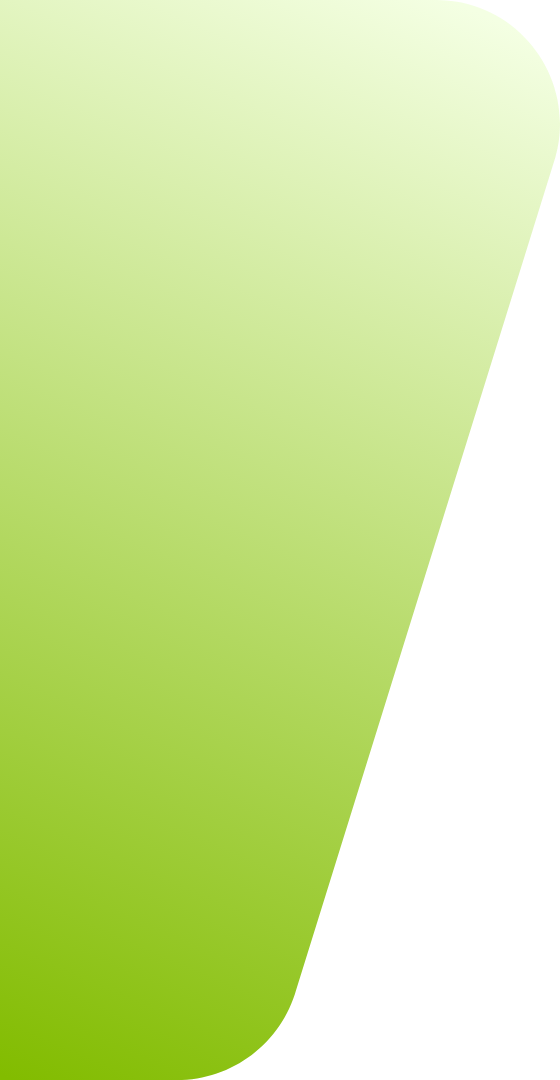
Highlights
-
In contrast to other highly automated profile wrappers, the RoboWrap takes into account the use-related shape change of the rolls
-
Profile programming and job lists can also be prepared from the desk
-
Intuitive and largely language independent operation of the software via drag and drop
-
Correction of roll positioning while the machine is running with a tablet and without manual intervention
-
New software calibrates the machine autonomously, new process also allows automatic process in start of operation
-
Reduction of rejects as the tasks of the roles are saved
-
Number of robots depends on customer's demands, expandable
-
Setup time is calculable, as it is constant and independent of profile geometry
-
No specialist personnel is required for the production
-
Significantly reduced risk potential, since no human intervention takes place
-
Permanent further development of the software with corresponding updates
-
Numerous patented system developments
-
Software also considers wear and tear of transport rollers when positioning pressure rollers to maximise accuracy